VISITE HAGER
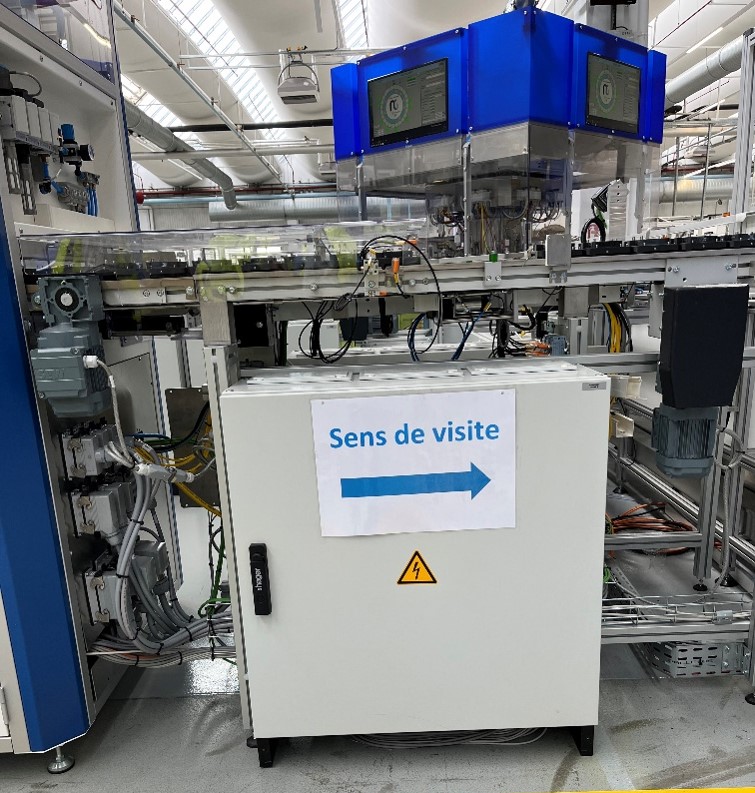
Vous étiez nombreux à nous avoir demander une visite d’usines … cette année le comité a eu l’opportunité d’organiser celle-ci.
Pour des raisons de sécurité, nous avons dû créer des groupes de 20 personnes par visite. Trois dates ont été retenues (le 27/06, le 02/07 et le 27/09) avec à chaque fois deux groupes de 20 personnes.
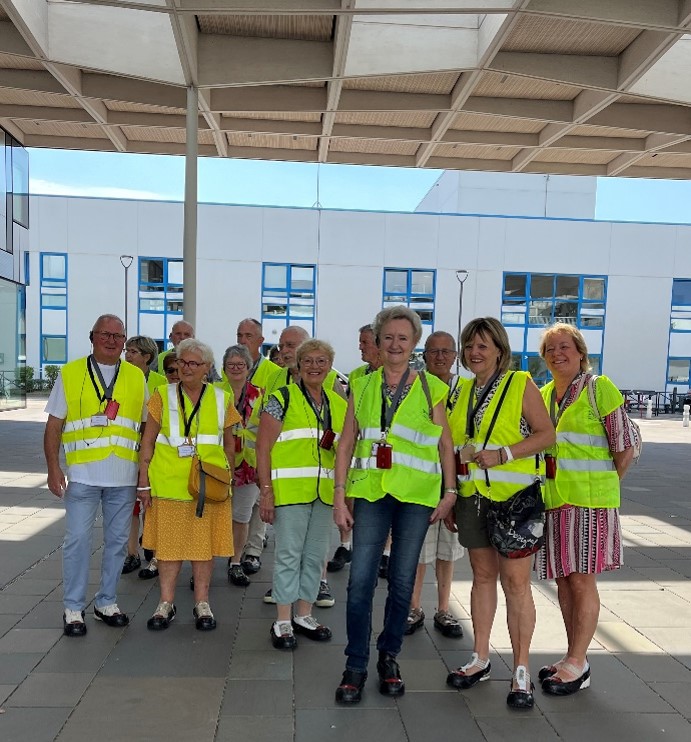
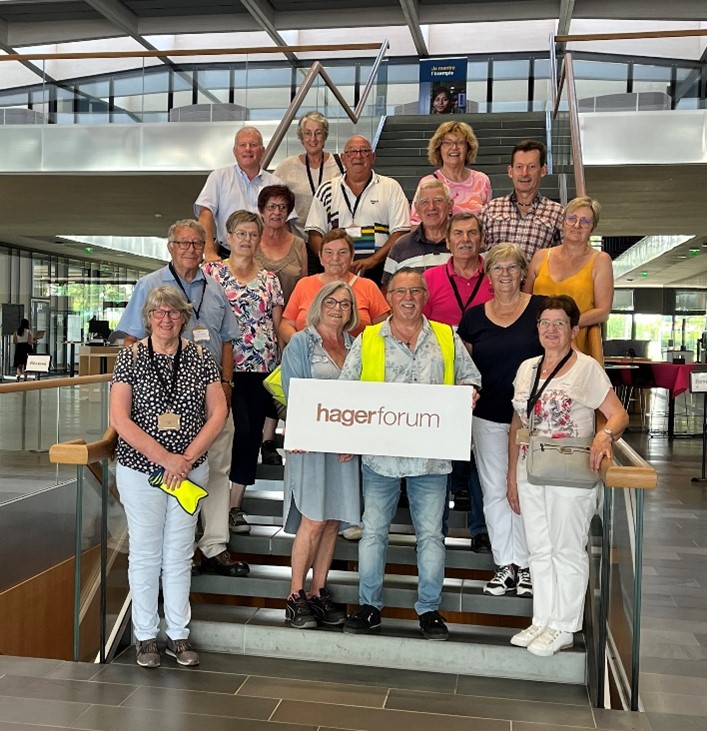
Equipé de nos gilets fluorescents, de nos chaussures de sécurités (ou sur-chaussures prêtées par l’entreprise) et de nos écouteurs , nous voilà parti pour une visite d’une heure !
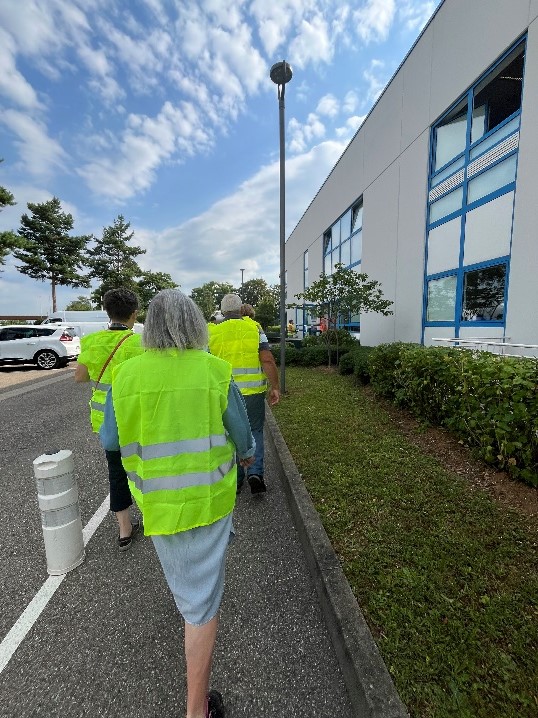
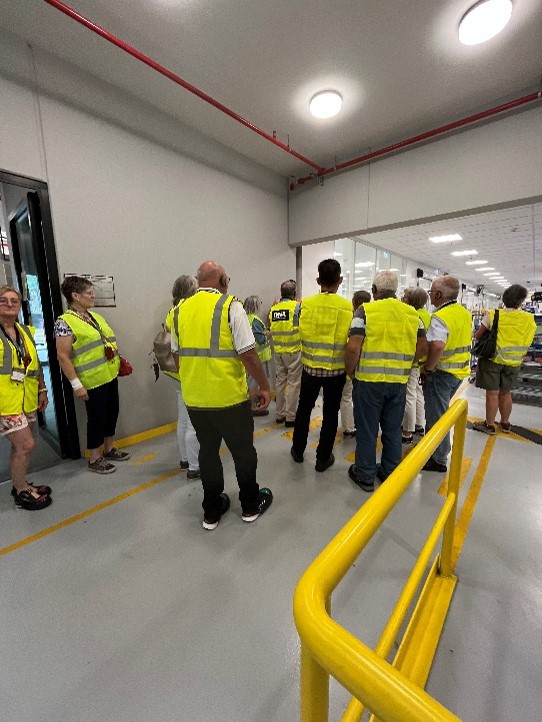
Le fil conducteur de notre visite était principalement lié aux nouveautés (nouvel atelier relais, l’assemblage U1 avec la nouvelle ligne BP4 ainsi que la ligne de finition et d’expédition (LFE), et pour finir le nouveau laboratoire baptisé TARANIS …
Le nouveau relais :
Qu’est-ce que le relais ?
C’est la pièce majeure des produits de protection des personnes (interrupteur ou disjoncteur différentiel).
En cas de fuite de courant à la terre (risque d’électrocution), l’appareil différentiel envoie une énergie électrique au relais qui provoque le déclenchement de l’appareil de protection différentielle.
Objectif du nouvel atelier de fabrication du relais.
1/ Augmentation de la production des relais : 200 000 relais produits par semaine.
2/ Obernai étant le seul fabricant de relais pour tout le groupe (clients : Obernai, Bischwiller, Pologne, Inde et Chine), il fallait créer un second atelier pour garantir la pérennité de la fabrication en cas de sinistre (Ex : incendie de l’atelier).
Secteur assemblage U1 :
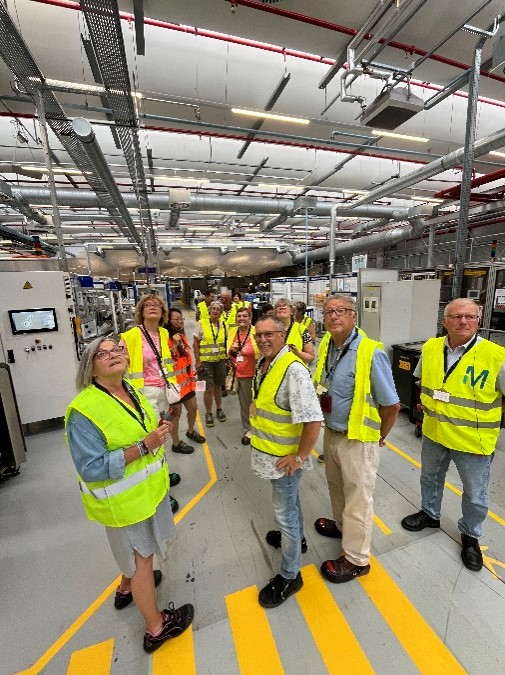
Le secteur réalise l’assemblage total en automatique ainsi que le réglage et contrôle des disjoncteurs destinés aux marchés européen (excepté la France : disjoncteur phase neutre fabriqué en U3), la Chine, l’Inde et l’Australie.
Trois lignes d’assemblage automatisées (BP2 et BP4 disjoncteurs unipolaires et BP3 disjoncteurs multipolaires).
BP2 et BP3 ont été installées en 2010 et 2011 pour une capacité de 42 pièces par minute.
BP 4 a vu le jour en 2024 pour une capacité de 45 pièces par minute
(Coût de l’investissement : 11 Millions d’euros).
La nouvelle ligne LFE (Ligne de Finition et d’Emballage) totalement automatisée d’une longueur de 70 mètres a été mise en service en mars 2024 pour un investissement de 5 millions d’Euros.
On y retrouve des opérations de marquages spécifiques.
En voici quelques-unes.
Etape 4 : Le logo Hager (tampographie).
Etape 5 : Marquage au laser de la manette.
Etape 7 : Marquage de la référence (laser).
Etape 10 : Marquage latéral « Made in France », n° de série, code-barre.
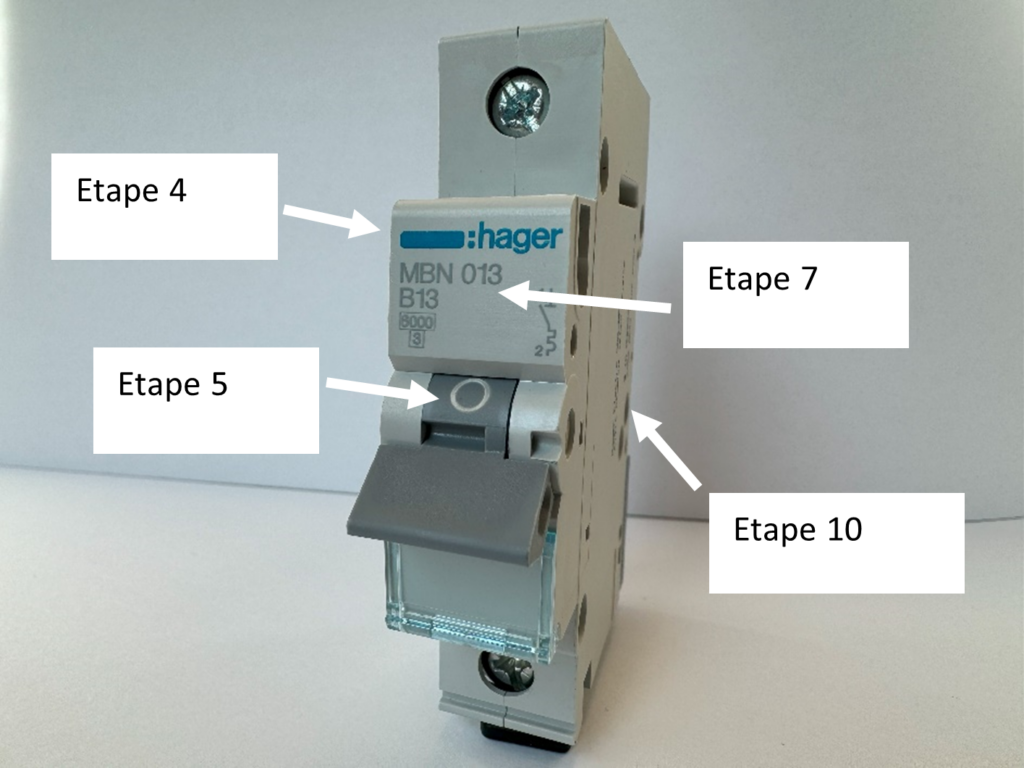
Les produits finis partent directement au centre de distribution de Vendenheim pour livraison chez le client final.
Le Laboratoire TARANIS :
Ce nouveau laboratoire a pour objectif d’acquérir une totale autonomie en termes d’essais laboratoire et de certification.
Le laboratoire actuel avec une capacité de 15 000 Ampères en court-circuit est suffisant pour nos appareils modulaires mais pour nos gammes supérieures (MCCB et ACB) nous sommes dépendant des sociétés SOCOMEC ou SAAT en Chine.
TARANIS avec une capacité de 150 000 Ampères, sera le plus performant du Grand-Est et l’un des plus puissants en Europe. Il permettra de développer et valider des disjoncteurs et des systèmes de distribution de forte puissance (appareillages de protection et armoires électriques).
Il intègre un alternateur de forme cylindrique de plus de 7 mètres de long et 3 mètres de diamètre, pesant plus de 100 tonnes.
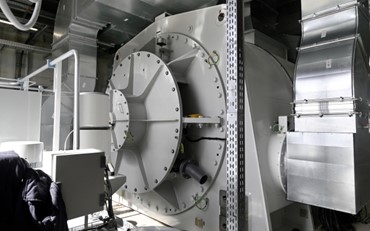
Coût du projet : 16 Millions € (avec soutien financier de la Région Grand Est)
A la fin de cette visite, beaucoup d’entre nous se sentaient fiers de ces projets et de constater que l’entreprise investie encore sur nos sites alsaciens …
Commentaires récents